盐城美国原装等离子切割用户体验
等离子切割的精度相对较低。一般来说,等离子切割的精度在1mm以内,切割速度也较快。但是,等离子切割的热效应明显,切割边缘容易产生热变形,对于一些高精度切割需求可能难以满足。此外,等离子切割还容易产生烟雾和噪音污染。激光切割的精度则较高。切口细窄,切缝两边平行并且与表面垂直,切割零件的尺寸精度可达±0.2mm。激光切割速度也较快,而且不会产生弧痕和热变形,对于一些高精度切割需求可以更好地满足。具体选择哪种切割方式还需要根据具体的切割要求和应用场景来决定。 海宝等离子切割机采用等离子弧放电技术,能够快速切割各种金属材料。盐城美国原装等离子切割用户体验
等离子切割
等离子切割的优点有:1.可以切割所有金属板,包括不锈钢、铝等材料。2.切割速度快、效率高、精度高。3.在切割厚板方面具有优势,因为等离子弧能量更集中,温度更高,可以达到非常高的切割速度。等离子切割的缺点有:1.切割过程会产生有害气体和电弧,会对环境造成一定污染。2.切割面垂直度差,可能会有较大的斜角。3.切割过程中会产生较多的切割渣,需要人工处理。4.等离子切割热影响区较大,切缝较宽,不适合切割薄板。5.刀具等消耗品消耗快,成本较高。 镇江小型等离子切割厂家供应维护保养:定期检查设备紧固件是否松动,切割头是否磨损,气管是否漏气等,并及时进行维修保养。
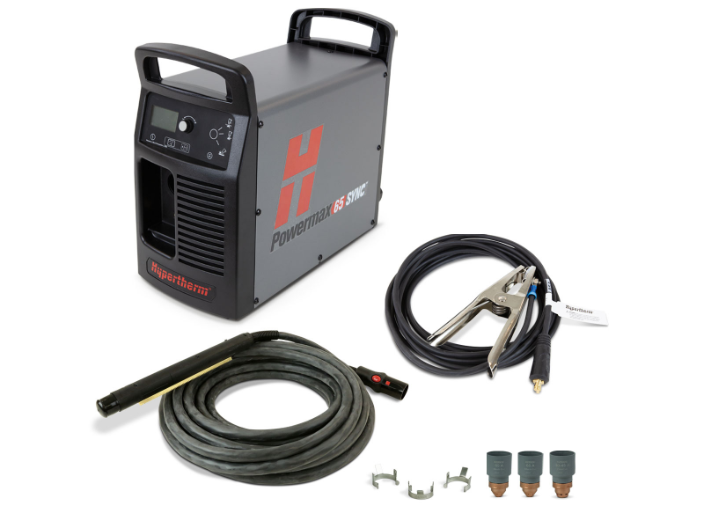
等离子切割的原理是利用高温等离子的电弧对金属材料进行局部加热和熔化,同时借助高速等离子的动量将熔融的金属材料排出形成切口。具体来说,等离子切割机利用高频电弧将气体原子电离成等离子体,等离子体中的高速带电粒子撞击工件时,动能转化为热能,使工件瞬间加热至熔点以上,同时将熔化的金属材料吹散。等离子切割机产生的等离子体温度可达数万度,能量密度极高,可以将金属材料瞬间加热至熔点以上,因此可以实现高效、高精度的切割。同时,由于等离子体具有一定的氧化性,可以对金属材料进行一定的热处理,提高材料的切割质量。在切割过程中,等离子切割机需要先通过气体引入系统将气体引入到切割头中,再通过高频电弧点燃将气体离子化。离子化的气体具有高能量密度和瞬间高温的特点,可以将金属材料瞬间加热至熔点以上,同时高速气流将熔化的金属材料吹散形成切口。因此,等离子切割的原理主要是利用高温等离子的电弧对金属材料进行局部加热和熔化,并通过高速等离子的动量将熔融的金属材料排出形成切口。
等离子切割是一种利用等离子体切割材料的技术。等离子体是一种高温、高能量的气体,由电离的气体分子和自由电子组成。在等离子体切割中,通过加热气体使其电离,形成等离子体,然后将等离子体喷射到要切割的材料上,利用等离子体的高能量将材料切割开。等离子切割具有以下几个作用:切割金属材料:等离子切割可以切割各种金属材料,包括钢铁、铝、铜、钛等。由于等离子体的高能量,它可以轻松地穿透金属表面并将其切割成所需形状。切割非金属材料:等离子切割还可以切割非金属材料,如陶瓷、玻璃、塑料等。随着技术的不断发展,海宝等离子切割机的性能也在不断提升。
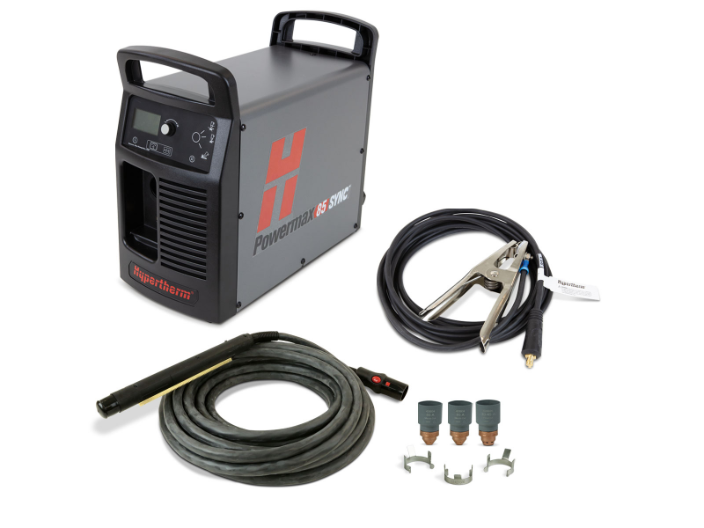
在等离子切割过程中,提高切割质量的方法包括:1.正确设置和调整切割参数。需要参照海别得使用手册“操作”一节中的切割表,根据不同的材料类型、厚度、所需切割质量以及目标生产率,选择适合的工艺、等离子气体和保护气体,并设定正确的参数,如气压(或流量)、割炬到工件的距离和弧压、切割速度等。2.确保易损件正确。易损件包括割炬、喷嘴和电极等,需要检查其是否磨损,并及时更换。一般来说,低电流工艺能够实现更好的切割角度和表面抛光,但切割速度会变慢且熔渣量增大。3.垂直切割。通过调平工件和使割炬垂直于工件(割炬前面和侧面),可以优化切割角度,提高切割质量。4.预留工艺小凸台。在设计切割时,不在零件的轮廓线上设置切割的起点和终点,而是加入工艺小凸台,将引入引出线交汇处搬移至零件轮廓外,从而减少后续打磨工作量,提高切割质量。以上是在等离子切割过程中提高切割质量的一些方法,可以结合实际情况和专业知识进行选择应用。 海宝等离子切割机具有自动识别功能,可以根据材料自动调整切割参数。苏州多功能等离子切割服务电话
海宝等离子切割机具有防尘、防水、防腐蚀等多重保护措施,使用寿命长。盐城美国原装等离子切割用户体验
海宝等离子切割机的切割速度可以通过以下方式提高:*选用合适的切割机型号。根据所要切割的对象的材质和规格,选择能够满足要求的切割机型号,以确保切割速度和效率能够达到预期目标。*调整切割头的传送速度。增加切割头的传送速度可以加快切割速度,从而提高切割效率。可以通过在控制面板上调整传送速度来达到期望的传送速度。在操作过程中,建议您根据实际情况选择合适的调整方法,并对设备进行合理定位,以保证切割的质量和效率。 盐城美国原装等离子切割用户体验
上一篇: 盐城美国原装海宝等离子厂家电话
下一篇: 盐城小型等离子切割厂家供应